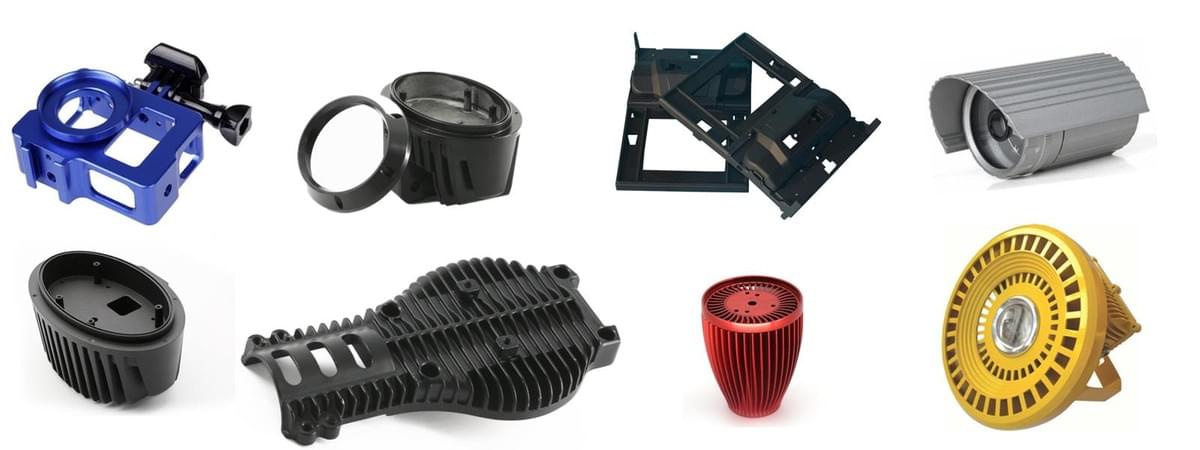
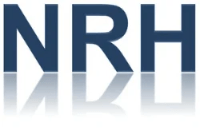
OEM SPECIALIST
High Pressure Die Casting
Plastic Injection
- Die casting is a fairly specialised process which has developed more predominantly within the 20th century. The basic process comprises of: molten metal is poured/injected into a steel mould and via high velocity, constant and intensifying pressure (in pressure die casting) and cooling the molten metal solidifies to form a solid casting. Typically, the process itself only takes a few seconds and is a quick way of forming metal product from raw material. Die casting is suited to materials such as tin, lead, zinc, aluminium, magnesium to copper alloys and even iron alloys such as stainless steel. The main alloys utilised today in pressure die casting are aluminium, zinc and magnesium. From the early die cast machines which orientated die tools in vertical orientation to the now common standard of horizontal orientation and operation, four tie bar tensioning and fully computer controlled process stages the process has advanced throughout the years.The industry has grown into a worldwide manufacturing machine, making components for a variety of applications, many of which will be in reach from ones self as the product application of die castings is so diverse.Benefits of pressure die castingSome of the benefits of high pressure die casting:The process is suited to high volume productionProduce fairly complex castings quickly compared to other metal forming processes (eg. machining)High strength components produced in the as cast condition (subject to component design)Dimensional repeatabilityThin wall sections possible (eg. 1-2.5mm)Good linear tolerance (eg. 2mm/m)Good surface finish (eg. 0.5-3 µm)
Hot Chamber Die Casting
The process of hot chamber pressure die casting involves the melting of metal ingot within a furnace which is situated close/integral to the fixed half platen of the die casting machine and injection of molten metal via a submerged plunger directly through the gooseneck and nozzle and into the die tool. The gooseneck and nozzle require heating to prevent metal freezing before it gets to the die cavity, the whole heating and molten metal element of this process is where the designation hot chamber comes from. The casting shot weight is dictated by the stroke, length and diameter of the plunger as well as the sleeve/chamber size and the nozzle also plays a part which should be considered upon die design. Once the metal has solidified in the die cavity (takes only a few seconds) the moving half platen of the machine of which the moving half of the die is fixed to opens and the casting is ejected off the die face and removed from the tool. The die faces are then lubricated via a spray system, the die closes and the process cycles again.Because of this “closed” metal melt/injection system and minimal mechanical movement hot chamber die casting can provide better economies for production. Zinc metal alloy is primarily used in hot chamber pressure die casting which has a fairly low melting point which offers further benefits for low wear on machines (pot, gooseneck, sleeve, plunger, nozzle) and also low wear on die tools (so longer tool life compared to aluminium die casting tools – subject to casting quality acceptance).Hot Chamber
Cold Chamber Die Casting
The name cold chamber comes from the process of molten metal being poured into a cold chamber/shot sleeve which is attached through the fixed half die platen to the back of the fixed half die tool. Molten metal holding/melting furnaces are typically located as close as is practical to the shot end of the die casting machine so that a manual operator or an automatic pouring ladle can extract the molten metal required for each shot/cycle with a ladle and pour the molten metal into a pouring hole within the sleeve/shot chamber. A plunger tip (which is a wearable and replaceable part, precision machined to the shot sleeve inner diameter with allowance for thermal expansion) connected to the ram of the machine pushes the molten metal through the shot chamber and into the die cavity. The die casting machine when prompted will conduct first stage to push the molten metal past the pouring hole in the sleeve. Further stages take place under increased hydraulic pressures from the ram to inject the molten metal into the die cavity. The whole process takes seconds, the quick and intensifying pressure as well as the drop in metal temperature causes the metal to solidify in the die cavity. The moving half platen of the die casting machine opens (of which the moving half of the die tool is fixed to) and ejects the solidified casting off the die face of the tool. The casting is removed, the die faces are lubricated with a spray system and then the cycle is repeated.Cold chamber machines are suited for aluminium die casting, parts on the machine (shot sleeve, plunger tip) can be replaced over time, sleeves can be metal treated to increase their durability. Aluminium alloy is melted in a ceramic crucible due to aluminium’s relative high melting point and the need to reduce the risk of iron pickup which is a risk within ferrous crucibles. Because aluminium is a relatively light metal alloy it affords casting of large and heavy die castings or where increased strength and lightness in die castings is required.Cold Chamber
Pressure Die Casting Tools
Overview of tool construction
A pressure die casting tool explained in simple terms: if you had a component that needed to be cast you decide where on the component you would split it in half, two blocks of steel would surround the component and meet flush around the component and where you have determined where the split on the component is, you “remove” the component and the void which remains is your die cavity. A die tool then requires an entry point and channel called a runner/feed for the molten metal to enter the tool and into the die cavity. The remaining basic requirement needed are small pockets or voids around the die cavity to allow the molten metal to push any air into once it has filled the die cavity, these are called overflows/vents which typically break off easily off the component after the metal has solidified. Die design (and component design for die casting) is considerably more complex than what is stated above and we will continue to go into more detail below.A die casting tool can be as small or large or as simple and complicated as required and is primarily dictated by the design of the component as well as economies for manufacturing, it is wise to learn about designing for die casting and working with an experienced pressure die caster such as Midland Pressure Diecasting when designing new components as a die casters input will be vital to development of component design for feasibility of production die casting. The following technical information we offer as a brief overview for designing for die casting, there is much more to component and tool design than what is outlined here and by working with Midland Pressure Diecasting we can offer more technical design input into any project and you can be assured that your project will be in safe hands.Die casting tool
A die casting tool comprises of two steel blocks which when assembled together form the complete die cavity required to cast a component. The split on the component has a direct bearing on the design of the die tool and can alter costs considerably as well as affect future tool maintenance and upkeep.A die casting tool can be manufactured from a range of tool steels and careful consideration should be made into the requirement of life expectancy of the tool. A designer needs to consider tool life, how long will the tool be in production? The volumes of die casting supply need to be considered as this will have an impact on the wear on the tool. The process of die casting means a die casting tool needs to be able to withstand quick temperature increases and sudden temperature decreases many times an hour, sometimes many times a minute, throughout a production run. For large scale operations this can be an ongoing non-stop cycle.Split line on casting
Because a die tool is effectively one tool split into two halves there must be a corresponding split (split line) on the casting. The position and location of the split line on the casting needs to be in the most effective place as to cause minimum disruption down the line. Having a split line on a face will leave a witness line which will require secondary process operations to remove if needed which adds to the cost of the component. If the witness line is on an a-face (highly cosmetic and expected to be free of defects) then it is advisable to design for the split line to be moved to another area on the casting, this principle is doubly applicable if the surface is required to be porosity free.The location on the split line will also have a bearing on the long-term condition of the die tool (and corresponding press clip/trimming tool where applicable – a secondary tool required for the removal of un-required excess metal such as the metal feed and overflows). Over time areas on the tool will be prone to die erosion and wear so consideration should be input at the design stage to have these in places where they will have minimal impact on the component requirement and application.A tool designer will provide recommendations for the best split lines but a component designer should also have some input in the best places to consider for product application and also assembly with mating components.Split line and witness line
Draft angle
One of the most basic principles in designing for a die casting is the provision for positive draft/draw taper. Avoid creating surfaces perpendicular to or with negative draft taper to the die face line, negative draft will be impossible to cast without additional sliding cores creating the feature, perpendicular surfaces do not allow the ideal condition to allow the die to open without potentially causing damage to the solidified casting and also damage to the casting upon ejection from the die face. Risk of sticking of metal to the die impression or dragging on the component may also occur due to not having enough draft taper on the component/die cavity impression. An allowance of at least 0.5 degree of draft taper (the more the better) will make a huge difference for casting consistency and production efficiency.Draft Angle
Section thickness
As with any design methodology consideration should be put into component geometry, why is the casting shaped as such, does the component need to be so “heavy.” The weight element is important in die casting (as with any process which requires the provision and processing of raw material). In first instance it determines how much material will be required in producing the part which constitutes towards the price of the casting. Die cast machines come in various sizes and configurations which determines whether they are capable of producing a die casting. Wall section of a casting has an impact on the tool design, how the molten metal will fill the cavity of the die, how the metal will solidify in the
die cavity, how long it will take to solidify etc.Wall thicknesses of 2-3mm for aluminium and 1mm for zinc are typical examples and are subject to the component design and application. Consideration for wall thickness should allow for radiuses where sections intersect at a sharp angle for strength of the component in that region, durability of that feature on the die tool and to aid in molten material flow within the die cavity. Ideally wall section thickness should be the same throughout the whole of the component (although in actual application this is sometimes difficult) as changing from thin section to thick section can cause cavity filling and surface finishing issues.The cavity in the die must be filled with metal very quickly, the general timing is between one hundredth and one tenth of a second and this is dependent on the casting size and design. The wall thickness aided with radiuses will allow smoother metal flow to minimise turbulence to prevent surface imperfections. A shorter die cavity fill time will aid in providing a better surface finish on the casting.Also when molten metal solidifies the volume of molten metal in the die cavity will shrink as it cools, liquid metal must be available to fill the space created otherwise a shrinkage void will remain which is why it is best to avoid sudden variations in wall thickness and avoid thick wall sections completely where practicable.Section Thickness
Avoiding undercut features (avoid the need for moving cores)
Consideration of complex/undercut features within the component design at early stages will save a lot of time later on. Complex forms, cored holes and undercuts can be a cast in feature and calls for the implementation of sliding cores which in one way can be designed to slide into position via angled guide pillars mounted onto one die half which locate the slide core blocks on the opposite die half to move into position when the die closes and opens. These slide cores can also be hydraulically operated with the use of cylinders. It is always preferred to avoid moving cores where possible as they add cost to the die tool, they reduce casting cycle times and they also add into the probability factor for operation and maintenance of the tool – they can be cause for variability on the casting dimensions which require stringent quality control monitoring for critical areas and because they are a moving part they are prone to wear and require maintaining.Avoiding Undercut Features
- Taking advantage of cored holesSecondary processing can be greatly reduced by using cores in the die tool to cast holes at the casting stage. Small holes can be cast in, they can also be cast without taper though consideration for tool life and maintenance as well as production need to be considered for viability to implement such casting designs.Strengthening ribsAn excellent alternative to having areas of thick material on a casting is to include strengthening ribs which will provide added strength to a component whilst in some applications also allowing the removal of material within the same region for the benefit of component weight reduction. The ribs should be designed in a way to allow molten metal flow to aid in die cavity filling, they should also be rounded and blended (with rads) to further enhance metal flow and reduce chances of the casting sticking to the die face upon metal solidification and ejection.
Avoiding Undercut Features
Design edges and features to prevent local die overheating
Small features/sections on a die impression such as a sharp edge or a protrusion such as a core for a hole may be prone to overheating which can lead to issues to cause drag marks and porosity depending on the component and how the die is designed. Such features should have thought put into alternative design as in the long run chances of tool breakage and maintenance can be vastly reduced to benefit in longer tool life.
Prevent Overheating
Required casting surface finish
Although smooth surface finishes on a casting are achievable as cast, certain applications may need additional machining in order to provide the desired surface finish. Further surface preparation is advisable for castings which require powder coating, an alternative feature is to add texture to the die surface but this is component dependent. For secondary processes such as linishing and polishing, where applicable simple, flat-section surfaces are preferred and areas with blind holes and recesses should be avoided as they tend to trap abrasive/polishing compounds which causes problems when plating parts. Large flat sections should be slightly curved (convex/concave) as they provide a smooth uniform surface to ease processing when linishing and polishing. Sharp junctions should be avoided in a casting required for electro plating as are blind holes, v-like grooves and upstands, such features should be designed with radiuses to allow even plating thickness to deposit, reduce plating times and increase durability of the plating, this also applies for castings which require powder coating. If lettering is to be cast in on a component these are better off to be a raised feature on the casting rather than sunk in, this will also benefit the durability of this feature on the die tool.
Casting threads
Threads in castings can be cast in, this is more suited to zinc die casting as the material allows for fine cast in detail. Consideration has to be put into production efficiency due to the configuration of the die tool required to cast threaded parts reduces the cycle time and makes the tooling more expensive.
Casting with inserts
Where required, for strength applications for example, inserts can be cast into a die casting. The die tool needs to be designed in a way which allows the insertion and retention of the inserts upon each die opening cycle and clearance for molten material to cast around the inserts sufficient enough to provide enough strength for their product application without breaking out the casting, consideration also needs to be made for correct seating so the insert is always cast in the correct position on every cycle. Casting with inserts slows down the cycle time which increases component cost so a designer should consider whether this is necessary at the cast stage or whether an insert can be assembled in a secondary process.
Casting Alloys
Midland Pressure Diecasting manufacture die castings for a range of applications in a variety of aluminium and zinc metal alloys. Our technical team can offer recommendations on casting materials which will meet your specifications for die cast product. If there is a specific casting alloy you need please feel free to contact us as we will be able to help with your supply requirements. The following technical descriptions define typically alloys utilised and the information is offered as a guideline only.
Aluminium Alloys
Aluminium alloy die casting contributes the largest percentage of material in die castings today. As the material and process has become better understood throughout the 20th century more and more uses of the material within die castings have developed. Aluminium offers strength properties above those for steel and iron as well as reduced weight which is why automotive is one of the largest industrial sectors with use of aluminium die castings.
Aluminium alloys are well suited to machining and can offer faster and easier machining solutions compared to other materials subject to utilising the ideal machining characteristics. Aluminium alloys compared to steel and cast iron do not suffer from ductile-brittle transformation so can be used in cryogenic applications without any sudden loss in ductility of impact strength. Aluminium is often chosen for it excellent resistance to corrosion, this is in part due to aluminium having a natural oxide film which develops when in contact with air which reforms if damaged, alloys with high content of silicon such as LM6 aid in corrosion protection and use of castings in outdoor environments and the material can also be powder coated, electro-plated or anodised for further corrosion protection.
Aluminium is an easily recyclable material hence its use in many applications.
LM-6
BS Ingot Colour Code: Yellow
LM 6 (BS 1490:1988) – (similar to EN AC/AB 44100/44000, (USA 369.1/A413/B413), (France AS12/13), (Italy UNI4514), Germany (AlSi12, 230), (Japan AC3A))
LM6 (Al-Si12 type) is one of the most widely used aluminium alloys in die cast production. Due to the high silicon content it has excellent fluidity for casting purposes and affords high resistance to corrosion. The alloy provides excellent pressure tightness and hot tearing properties. The material can be machined and care must be taken in utilising the correct tools to minimise wear due to the high silicon content. LM6 is suited to post casting finishing such as powder coating, electro plating and anodising which further enhances its corrosion resistance properties in real world applications.
Alloy composition
Symbol
Min %
Max %
Magnesium
Mg
–
0.10
Silicon
Si
10.0
13.0
Titanium
Ti
–
0.2
Manganese
Mn
–
0.5
Iron
Fe
–
0.6
Nickel
Ni
–
0.1
Copper
Cu
–
0.1
Zinc
Zn
–
0.1
Tin
Sn
–
0.05
Lead
Pb
–
0.1
Others (Total)
–
0.15
Aluminium
Al
Remainder
Typical physical and mechanical properties (as cast)
Casting Temperature
-725 °C
Freezing Range
565-575 °C
Thermal Conductivity at 25 °C
0.34 cal/cm2/cm/°C
Coefficient of Expansion per °C at 20-100 °C
20 x 10-6
Electrical Conductivity
37% IACS
Density
2.65 g/cm3
0.2% Proof Stress
120 N/mm2
UTS
280 N/mm2
Elongation
2-5%
Hardness
55-60 BHN
LM-24
BS Ingot Colour Code: Red/Blue
LM 24 (BS 1490:1988)– (similar to EN AC/AB 46500, (USA 380/A380/B380), (France AS9U3Z), (Italy G-AlSi8.5Cu), Germany (G-AlSi8Cu3, 226), (Japan AC4B, AD10))
LM24 (Al-Si8Cu3Zn type) is the most widely used aluminium alloy in die cast production together with LM2 they are equally suitable for most applications of die castings. This alloy is highly suited to machining and has better mechanical properties than LM6, its corrosion resistance is good in normal atmospheric conditions and can be further improved via post cast finishing such as powder coating and anodising. It offers excellent pressure tightness and hot tearing properties.
Alloy composition
Symbol
Min %
Max %
Magnesium
Mg
–
0.30
Silicon
Si
7.5
9.5
Titanium
Ti
–
0.2
Manganese
Mn
–
0.5
Iron
Fe
–
1.3
Nickel
Ni
–
0.5
Copper
Cu
3.0
4.0
Zinc
Zn
–
3.0
Tin
Sn
–
0.2
Lead
Pb
–
0.3
Others (Total)
–
0.50
Aluminium
Al
Remainder
Typical physical and mechanical properties (as cast)
Casting Temperature
-700 °C
Freezing Range
520-580 °C
Thermal Conductivity at 25 °C
0.23 cal/cm2/cm/°C
Coefficient of Expansion per °C at 20-100 °C
20 x 10-6
Electrical Conductivity
24% IACS
Density
2.79 g/cm3
0.2% Proof Stress
150 N/mm2
UTS
320 N/mm2
Elongation
1-3%
Hardness
85 BHN
Zinc Alloys
Zinc alloy (also commonly referred to/identified/prefixed as ZL, ZA, Mazak, Zamak) is one of the most widely used materials for die castings in the world. The properties of zinc alloy make the material well suited for die castings required for decorative purposes and functional applications, the economics of zinc die casting are also very favourable. The hardness and dimensional stability of zinc make the material suitable for parts which are required in mechanical assemblies, its thermal and electrical conductivity make it a good choice for electrical component application as well as providing electromagnetic shielding. Zinc alloys (especially the ZA12 alloy) are non-sparking and are suited for applications within hazardous environments such as mines and fossil fuel refineries. Zinc castings are highly versatile for post cast surface finishing and can be made to look like other materials/cosmetically aged via painting and plating as well as other industrial/chemical processes.
Due to the fairly low melting point for zinc compared to other metal alloys there are significant energy savings as well as the reduced impact on the environment. The lower temperatures also mean there is less of a thermal impact on tool steel, therefore providing die life advantages over other casting materials. Zinc is one of the cleanest materials to use for molten processing purposes and is easily recyclable.
ZL-3
BS EN Ingot Colour Code: White/Yellow
ZL 3 (BS EN 1774:1997) – (similar to ZA3, Mazak 3, Zamak 3)
ZL3 is widely used as a general purpose zinc alloy for the hot chamber pressure die casting process. The alloys properties ensure its wide application of uses within the automotive and engineering industries. ZL3 is widely used within the hardware and lock industries as well as for industrial fixings, furniture fittings, toys etc. The chemical composition of ZL3 conforms to the BS EN 1774:1997 standard which is widely standardised across Europe.ZL3 is suited for machining, polishing, lacquering, powder coating and electro plating – if a high cosmetic plating finish is required zinc is recommended.
Alloy composition
Symbol
Min %
Max %
Magnesium
Mg
0.035
0.06
Aluminium
Al
3.8
4.2
Silicon
Si
–
0.02
Iron
Fe
–
0.020
Nickel
Ni
–
0.001
Copper
Cu
–
0.03
Cadmium
Cd
–
0.003
Tin
Sn
–
0.001
Lead
Pb
–
0.003
Zinc
Zn
Remainder
Typical physical and mechanical properties (as cast)
Casting Temperature
405-425 °C
Freezing Range
382-387 °C
Specific Heat
0.4187 J/gk (0.10)
Solidification Shrinkage
1.17 cm/m (0.14 in/ft)
Casting Shrinkage
0.006 mm/mm (0.006 in/in)
Thermal Conductivity at 18 °C
113 W/m°C (0.27 CGS)
Linear Thermal Expansion per °C
28 x 10-6
Electrical Conductivity at 20 °C
26% IACS
Specific Gravity
6.7
Density
6,700 Kg/m3 (0.24 lb/in3)
Tensile Strength at 20 °C
241-283 N/mm2 (41,000 lbf/in2)
Elongation at 20 °C
10-16% %in 2in
Impact Strength at 20 °C (un-notched)
56.9 J (42 ft.obf)
Hardness
82-87 BHN
ZL-5
BS EN Ingot Colour Code: White/Black
ZL 5 (BS EN 1774:1997) – (similar to ZA5, Mazak 5, Zamak 5)
ZL5 is used within the hot chamber die casting process whereby a stronger alloy than ZL3 is required. It is used where critical dimensional accuracy isn’t too important (don’t forget zinc is easily machined if needed) but strength and hardness is more of a factor in the end product. ZL5 is also suitable where small details in castings is a requirement or where surface preparation for plating using other zinc alloys is an issue. ZL5 is more expensive than ZL3 due to the higher copper content. The chemical composition of ZL5 conforms to the BS EN 1774:1997 standard which is widely standardised across Europe.
ZL5 is suited for machining, polishing, lacquering, powder coating and electro plating – if a high cosmetic plating finish is required zinc is recommended.
Alloy composition
Symbol
Min %
Max %
Magnesium
Mg
0.035
0.06
Aluminium
Al
3.8
4.2
Silicon
Si
–
0.02
Iron
Fe
–
0.020
Nickel
Ni
–
0.001
Copper
Cu
0.7
1.1
Cadmium
Cd
–
0.003
Tin
Sn
–
0.001
Lead
Pb
–
0.003
Zinc
Zn
Remainder
Typical physical and mechanical properties (as cast)
Casting Temperature
405-425 °C
Freezing Range
379-388 °C
Specific Heat
0.4187 J/gk (0.10)
Solidification Shrinkage
1.17 cm/m (0.14 in/ft)
Casting Shrinkage
0.006 mm/mm (0.006 in/in)
Thermal Conductivity at 18 °C
108.9 W/m°C (0.26 CGS)
Linear Thermal Expansion per °C
28 x 10-6
Electrical Conductivity at 20 °C
26% IACS
Specific Gravity
6.7
Density
6,700 Kg/m3 (0.24 lb/in3)
Tensile Strength at 20 °C
270-328 N/mm2 (47,000 lbf/in2)
Elongation at 20 °C
7-13% %in 2in
Impact Strength at 20 °C (un-notched)
54-65 J (43 ft.obf)
Hardness
80-92 BHN
© 2022 NINGNO NRH M&E CO.,LTD. ISO 9001:2015